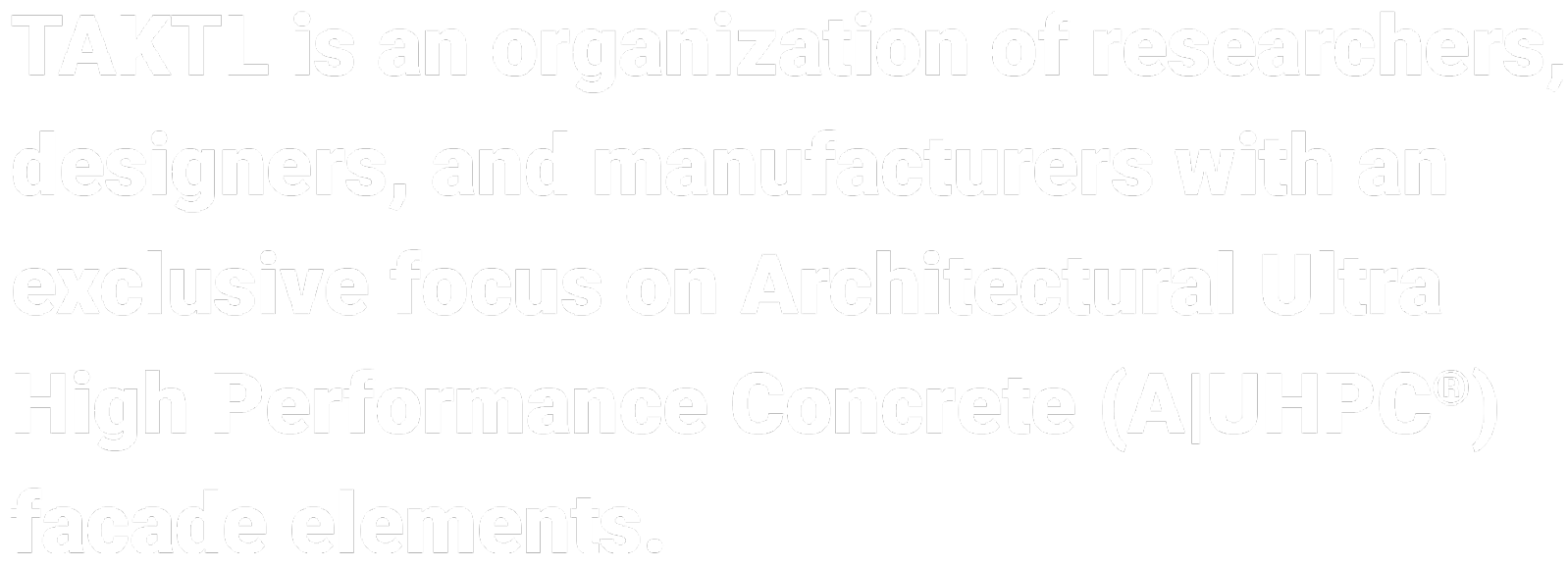
Our culture is one of curiosity and collaboration. Backed by research and driven by the world’s first vertically integrated UHPC manufacturing facility, we control every aspect of TAKTL’s design and fabrication and consistently deliver the highest quality A|UHPC facade elements in the world.
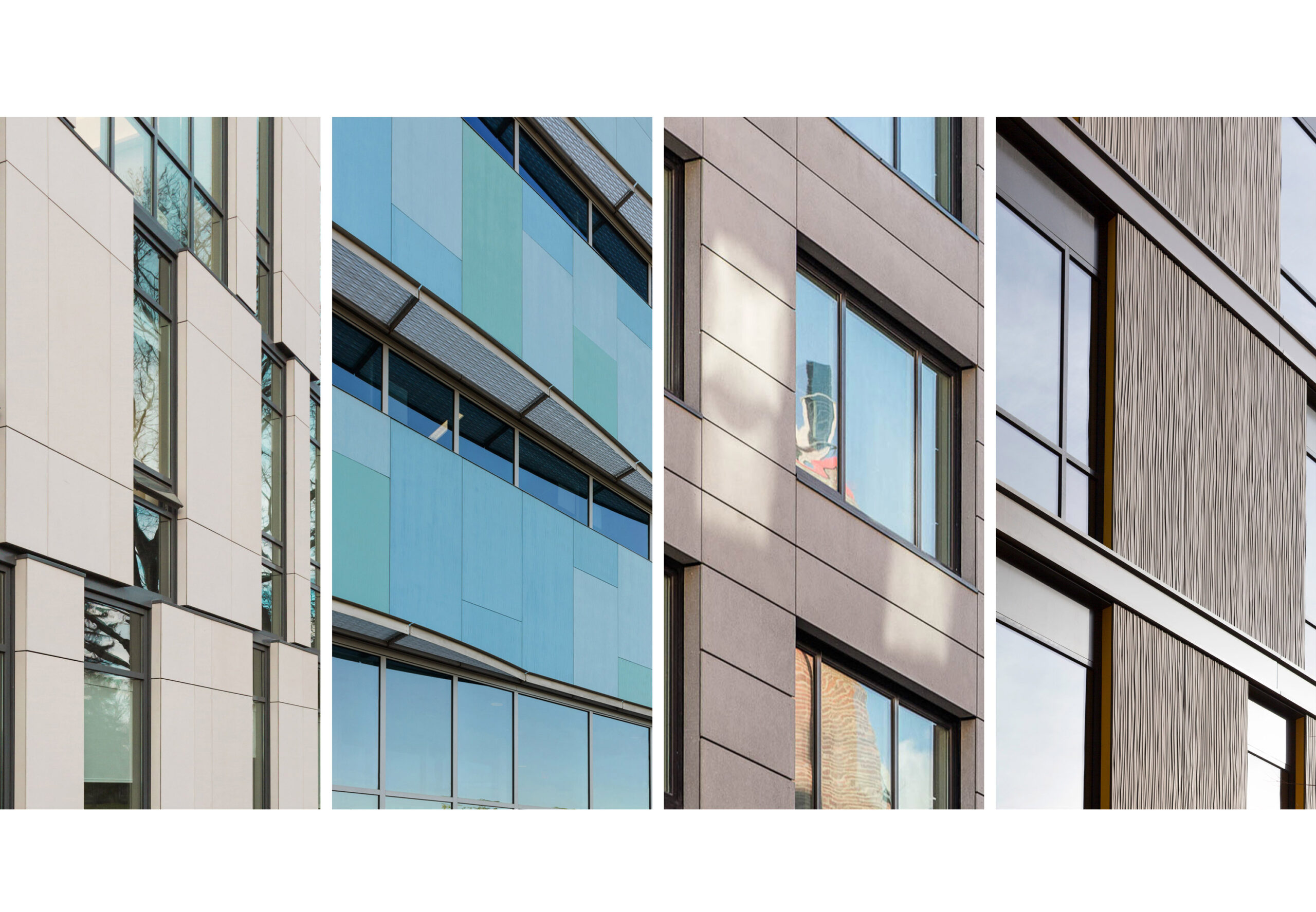
We are manufacturers producing custom A|UHPC facades with enduring quality and beauty.
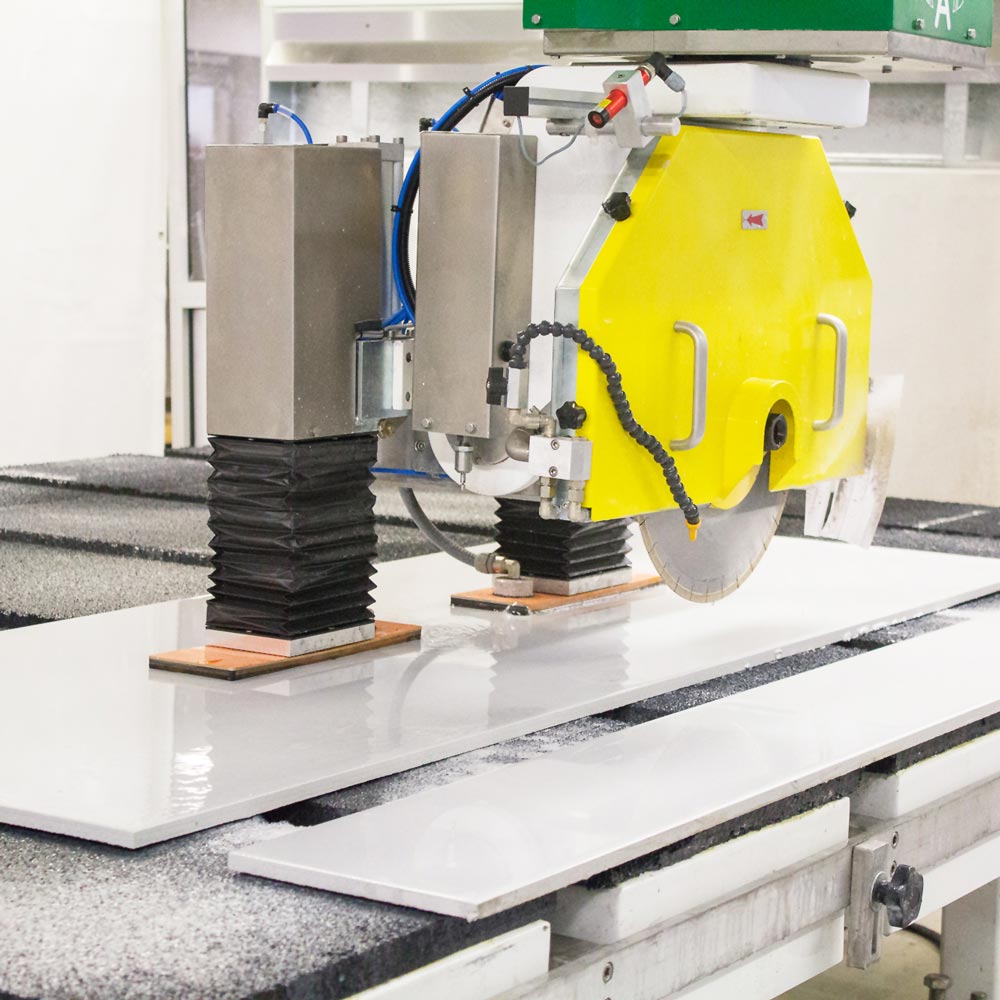
We are researchers making a tangible impact on carbon reduction in the built environment.
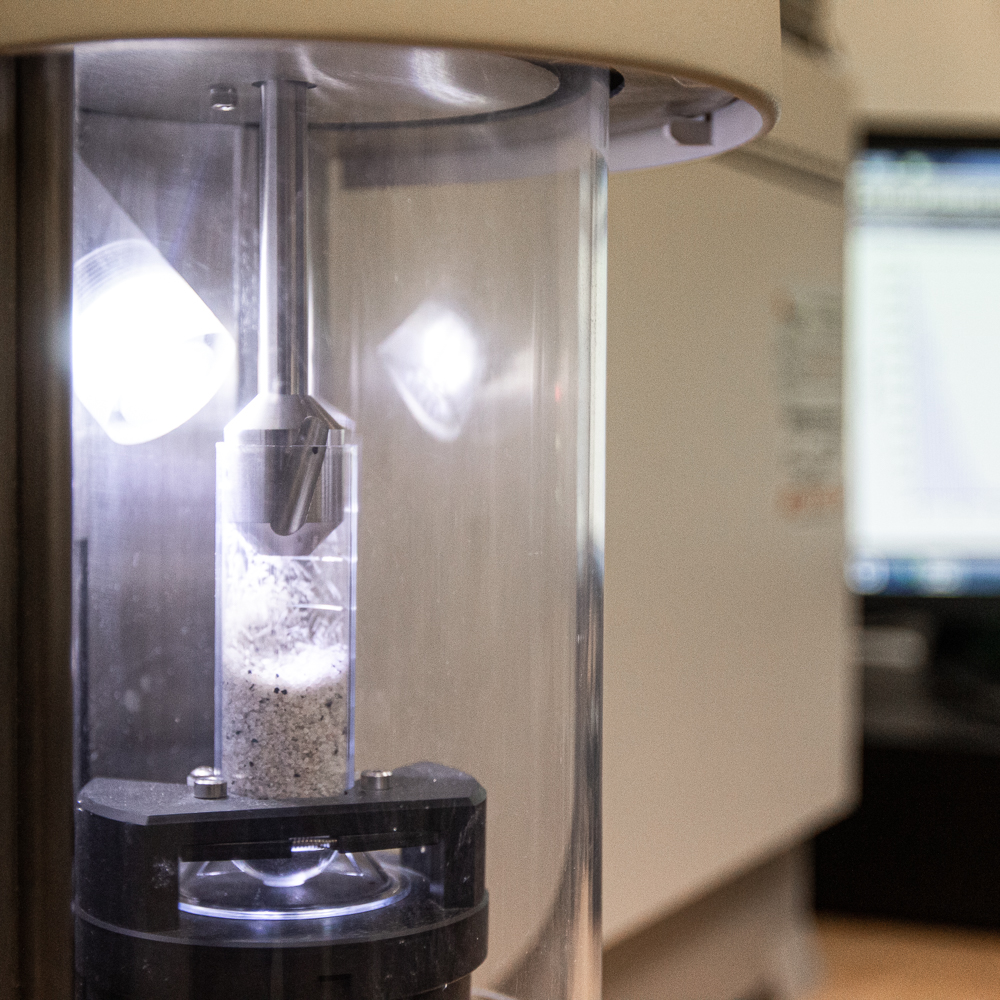
We are designers working as collaborators from the earliest stages of architectural projects.
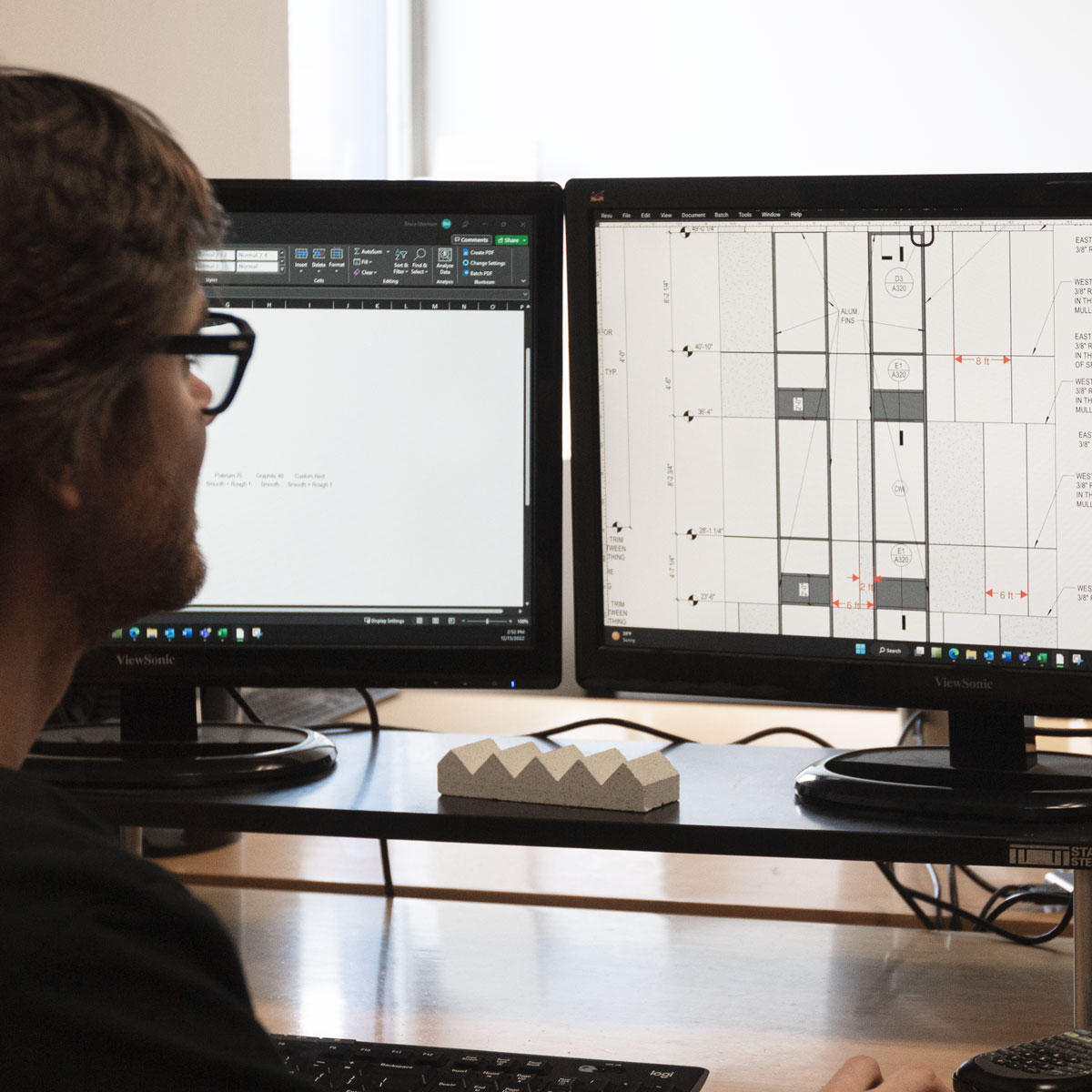
We are partners ensuring quality and communication in facade design and delivery.
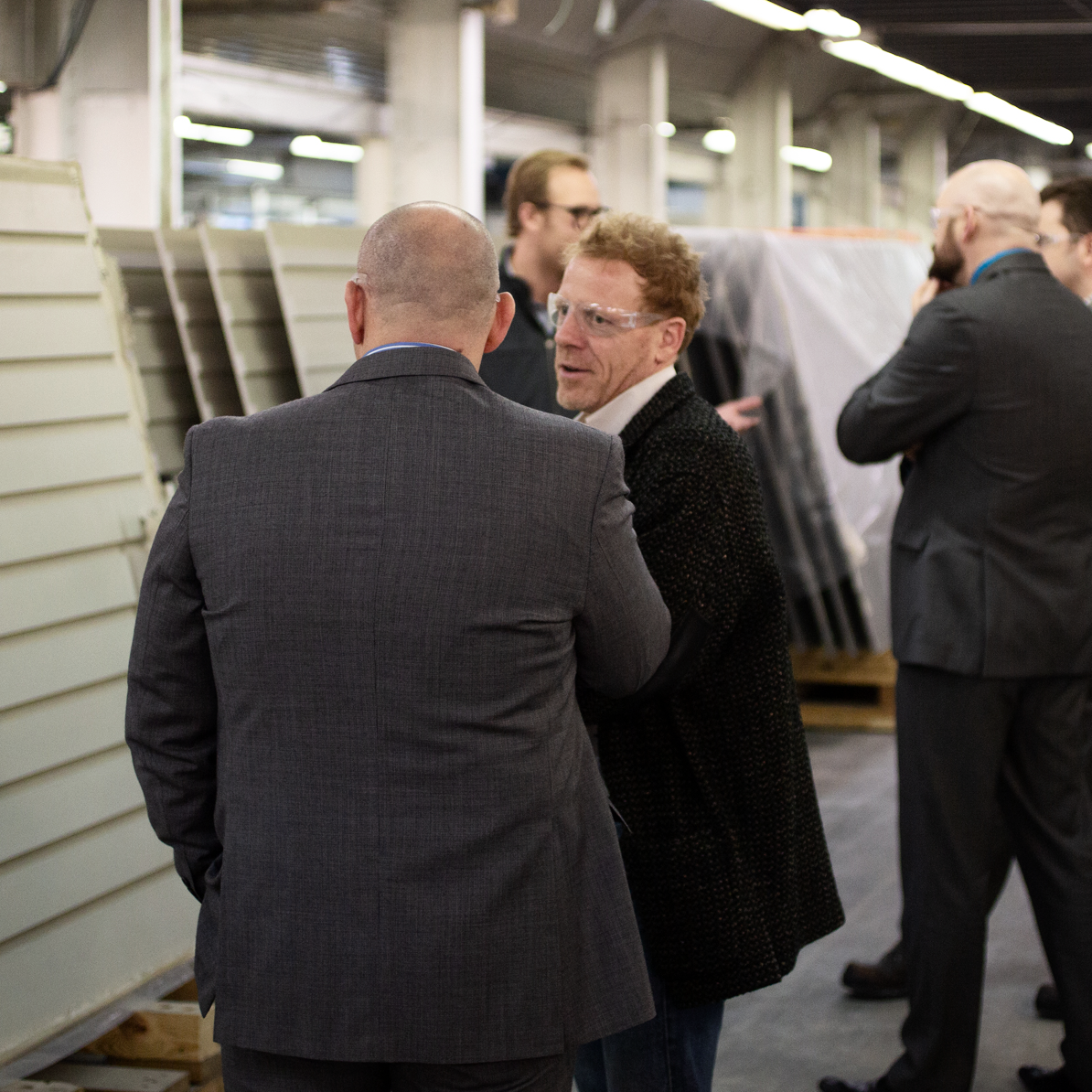